Metal Building Installations: What to Expect
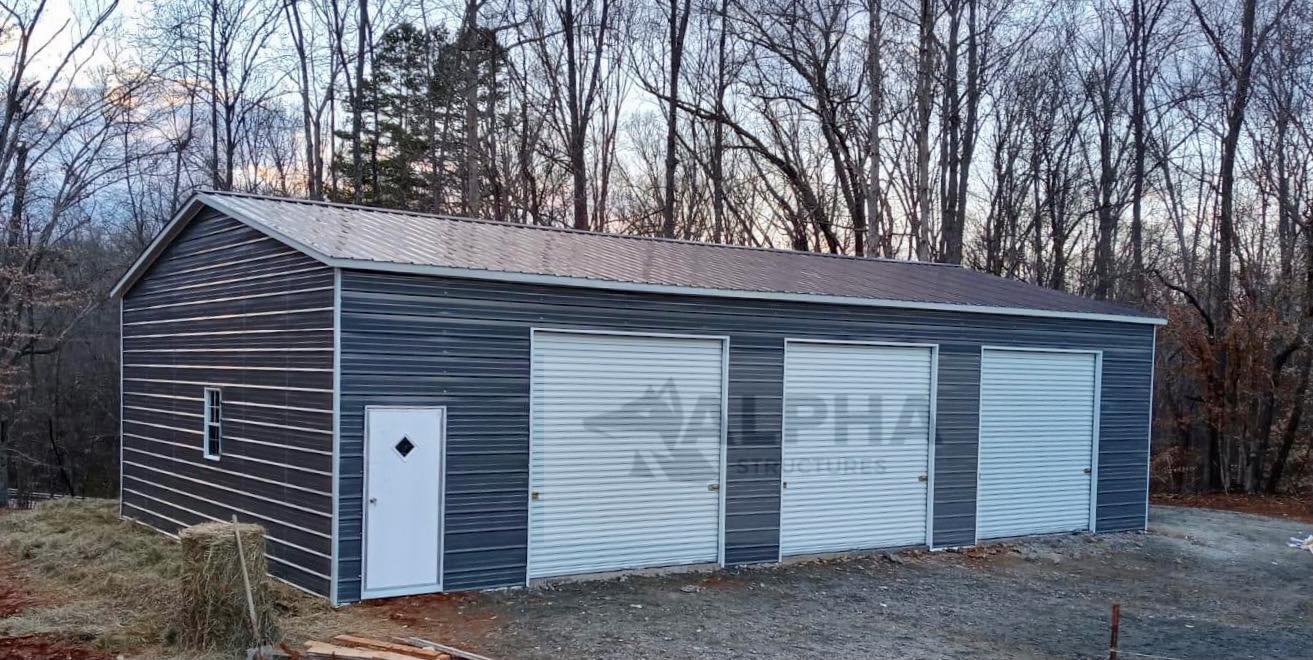
Metal buildings have a stellar reputation for low maintenance and durability—and they’re also easier to install than structures made with other materials.
In a prefabricated metal building, companies engineer each component to fit together. The pre-cut and pre-drilled framing pieces assemble quickly and easily. But there are a few factors to consider before installing a metal building. Paying attention to these considerations in advance can help ensure a seamless and hassle-free installation process.
Consider the Cost
When buying a metal building, many people only focus on price. For example, they wonder how much a 20-foot by 20-foot building costs compared to a 50-foot by 100-foot structure.
Basing your metal building purchase on price alone can be a mistake. Customers may select the lowest bid, only to find that the cost solely includes the kit. Many manufactures do not include installation and delivery costs.
Choosing a metal building supplier that includes installation and delivery in the purchase price eliminates the hassle. You know the total cost for your new metal building upfront.
The included installation fee will vary, depending on the structure you choose. The building’s overall size—and the wider the clear span—impacts the cost. A 12-foot-long by 24-foot-wide carport (similar in size to a two-car garage) is the most affordable option. But clear span can go up to 80 feet wide. These commercial buildings might cost $20,000 all in.
Selecting a barn-style metal building can control total costs for commercial buildings with larger clear spans. The barn divides into three sections, each a standard carport. Installers combine the sections into a single structure to make the building more affordable.
Get a Permit
Permit laws vary from state to state and municipality to municipality. It’s important to check on the laws in your area before getting the building installed.
Often, people do not want to pull a permit for their building. They own a bunch of land and believe no one will find out. And they may be right. But if the city enforces its permit policy, they may require the owner to tear it down.
The best way to avoid this scenario is to apply for a permit before the installation. Most local municipalities require engineered plans to secure the permit.
Engineered plans provide detailed information about the metal building. How it’s constructed, how it’s connected, where it’s welded and bolted together, and how it’s drilled into the ground. Your metal building supplier can provide these plans for an additional fee.
Prep the Build Site
A metal building must rest on a firm surface. This requires preparing the site before installation begins.
Leveling the area is the first step to good site preparation. Without a level surface, the building cannot go up. Get a professional measurement of your site before purchasing a metal building to ensure you have a large enough flat area for the building.
And remember—just because your site looks level doesn’t mean it is. Hire a professional to level the area before your installation crew arrives. If installers arrive and the site isn’t level, they will delay your installation.
Your building’s foundation can be gravel, dirt, wood, or concrete, depending on its size. A commercial building needs at least concrete strips around the building’s outside base, though you may prefer a concrete pad to dirt underneath your feet while working within the building. Remember to pour concrete at least 72 hours before installation.
Access to electricity is also a consideration. Installers may need access to electricity as they do the work, though most will bring a generator along.
Other Metal Building Installation Considerations
Call the utility company before digging on the property. Making this call ensures the safety of all involved in the installation. Usually, these entities will inspect your property for hidden wires and other dangers at no cost.
The county surveyor’s office offers a treasure trove of information about your property. A quick visit to the local office can provide information about flood zones, average snowfalls, wind speeds, and more.
You’ve Purchased the Building. Now What?
Once you’ve purchased the building, your manufacturer will reach out to confirm receipt of the order, estimate the delivery time (which averages four to six weeks), and discuss installation preparations.
After your site is prepped and the surface laid, it’s time to schedule installation. The manufacturer will supply an installation date.Your manufacturer will call to confirm installation time five days prior to ensure someone is there the day of installation. Weather permitting, the installation should take place as scheduled.
Installation typically takes one to five days, depending on the building size. For example, a standard carport goes up within a day, while a larger commercial building could take three to a week to install.
When your building is up, and you’re a satisfied customer, call the manufacturer and review the installation team. Manufacturers want to know that the installers they work with perform well and provide great customer service.
Getting a permit, properly prepping the site, contacting the local utility services, and working with your manufacturer ensures your new metal building will go up without a hitch.
Comments
Recent posts
-
4 REASONS WHY STEEL STORAGE BUILDINGS OUTPERFORM WOOD GARAGES A metal garage is the greatest way to ensure that your automobiles and workplace... December 11, 2022
-
Top 7 Uses for a Small, Attractive Commercial Metal Building You know that old saying, "size doesn't matter?" Well, that rings true for comme... December 11, 2022
-
Do Steel Storage Buildings Add Home Value: 7 FAQ Answered Adding a garage to your property is one of the smartest investments you can make... November 28, 2022